Luthier
Denis Wardlow started playing the violin at age seven with an old, beat up
violin and when he was 12, his mother gave him a better one, which became his
prized possession. He played frequently until 17, when he left home to complete
an apprenticeship in traditional small wooden boat building.
Unfortunately,
his prized violin was stolen from his home in 2001. Fortunately, Wardlow’s
daughter later gave him an inspirational gift; a book written in 1885 called Violin Making As it Was and Is. The book
provided history, references and instructions on violin making. Since Wardlow possessed
woodworking skills from years of boat building, he decided to make his first
violin in 2002. It was a success and he was hooked!
Violins are made from figured or flamed
maple for the back, ribs and neck and fine-grained Alpine, Sitka or Engelmann
Spruce for the top. The fingerboard is made of ebony. Most violins are
factory-made where artisans specialize in making one part. Modern machinery
produces complex shapes in minutes, which would take a skilled artisan many
hours. He must select a design then make a template and mould. The wood must be
chosen and cut to ensure correct grain direction to make for a good acoustical
response when tapped. Ribs are made of maple and are heat-bent to fit the
mould. The top and back are shaped to the desired outline and carved to
longitudinal and transverse curves of the design. A channel is cut around the
outer perimeter to receive a decorative and structural inlay – purfling
– preventing cracks.
Graduations of thickness are important. When
tapped, plates produce a musical note and the builder controls the note by
adjusting thickness in various areas of the plate. No nails or screws are used.
The glue is made from animal hides and tissues and can be unglued with hot water
to modify the instrument. The neck, pegbox and scroll are carved from maple. Holes
are made for pegs to adjust string tension to tune. The ebony fingerboard is
shaped, contoured and glued to the neck. The instrument is best varnished with
oil-based varnish.
Bows are made in various styles. The best
wood to use for bows is Pernambuco, which is in short supply. Today, bows are
often made from carbon fibre.
Violins have not changed much since the 16th
century when perfected by old Italian masters such as Amati, Stradivari and the
Guarneris. Sizes do not vary much and no two violins are the same.
A fiddle and a violin are the same
instrument, but may be set up differently. The fiddle is associated with
traditional folk music. A violin can fit in with classical, folk, country,
jazz, rock and pop music.
Wardlow has lovingly
made violins for personal enjoyment, for others to enjoy and created different
models that were inspired by Stradivari and Guarneri. In particular, he made
one to be used at a music school by promising students who could not afford a
good violin. The violin is not the easiest instrument to play as a violinist’s
fingers must find the right position for each note, while the other arm
coordinates bow movement.
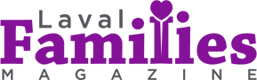
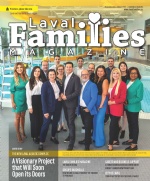
- A Bittersweet Farewell
- The new Laval Aquatic Co...
- The End of an Era:
Articles
Calendar
Virtual- ANNUAL TEACHER APPRECIATION CONTEST
- APPUI LAVAL
- ARTS & CULTURE
- CAMPS
- CAR GUIDE
- CCIL
- CENTENNIAL ACADEMY
- CHARITY FUNDRAISING
- CITYTV
- COSMODÔME
- COMMUNITY CONNECTIONS
- COVER STORY
- DINA DIMITRATOS
- ÉCOLE SUPÉRIEURE DE BALLET DU QUÉBEC
- EDITORIALS
- ÉDUCALOI
- EDUCATION
- EMPLOYMENT & ENTREPRENEURSHIP
- FÊTE DE LA FAMILLE
- FÊTE DU QUARTIER SAINT-BRUNO
- FAMILIES
- FESTIVAL LAVAL LAUGHS
- FÊTE DE QUARTIER VAL-DES-BRISES
- FINANCES
- GLI CUMBARE
- GROUPE RENO-EXPERT
- HEALTH & WELL-BEING
- 30 MINUTE HIT
- ANXIETY
- CHILDREN`S HEALTH & WELLNESS
- CLOSE AID
- DENTAL WELLNESS
- EXTREME EVOLUTION SPORTS CENTRE
- FONDATION CITÉ DE LA SANTÉ
- GENERAL
- HEARING HEALTH
- MESSAGES FROM THE HEALTH AGENCY OF CANADA
- MENTAL HEALTH
- SEXUALITY
- SOCIAL INTEGRATION
- SPECIAL NEEDS
- TEENS
- THE NUTRITION CORNER
- THE NUTRITION CORNER - RECIPES
- VACATION DESTINATION
- WOMEN'S FITNESS
- WOMEN'S HEALTH
- HILTON MONTREAL/LAVAL
- HOME & GARDEN
- INTERNATIONAL WOMEN'S DAY
- JAGUAR LAVAL
- LAVAL À VÉLO
- LAVAL FAMILIES TV SHOW
- LAVAL FAMILIES MAGAZINE CARES
- LAVAL URBAN IN NATURE
- LE PARCOURS DES HÉROS
- LES PETITS GOURMETS DANS MA COUR
- LEON'S FURNITURE
- LEONARDO DA VINCI CENTRE
- LFM PREMIERES
- LIFE BALANCE
- M.P. PROFILE
- MISS EDGAR'S AND MISS CRAMP'S SCHOOL
- MISSING CHILDREN'S NETWORK
- NETFOLIE
- NORTH STAR ACADEMY LAVAL
- OUTFRONT MEDIA
- PASSION SOCCER
- PARC DE LA RIVIÈRE-DES-MILLE-ÎLES
- PÂTISSERIE ST-MARTIN
- PIZZERIA LÌOLÀ
- PLACE BELL
- PORTRAITS OF YOUR MNA'S
- ROCKET DE LAVAL
- SACRED HEART SCHOOL
- SCOTIA BANK
- SHERATON LAVAL HOTEL
- SOCIÉTÉ ALZHEIMER LAVAL
- STATION 55
- STL
- SUBARU DE LAVAL
- TECHNOLOGY
- TEDXLAVAL
- TODAY`S LAURENTIANS AND LANAUDIÈRE
- TODAY`S LAVAL
- WARNER MUSIC
- THIS ISSUE
- MOST RECENT
Magazine
A Passion for Violins
Articles ~e 105,7 Rythme FM 4 chemins Annual Teacher Appreciation Contest Appui Laval Arts & Culture Ballet Eddy Toussaint Camps THIS ISSUE MORE...
CONTESTS Enter our contests
CONTESTS Enter our contests
CALENDAR
Events & Activities
COMMUNITY Posts Events
PUBLICATIONS Our Magazine Family Resource Directory
LFM BUSINESS NETWORK Learn more
COUPONS Click to save!
COMMUNITY Posts Events
PUBLICATIONS Our Magazine Family Resource Directory
LFM BUSINESS NETWORK Learn more
COUPONS Click to save!
SUBSCRIPTIONS
Subscribe to the magazine
Un-Subscribe
E-NEWSLETTER Subscribe to our E-newsletter Un-Subscribe
WRITE FOR US Guidelines & Submissions
POLLS Vote today!
E-NEWSLETTER Subscribe to our E-newsletter Un-Subscribe
WRITE FOR US Guidelines & Submissions
POLLS Vote today!
ADVERTISERS
How to & Media guide
Pay your LFM invoice
SUGGESTIONS Reader's Survey Suggest a Listing
LFM About Us Our Mission Giving Back Contact Us
SUGGESTIONS Reader's Survey Suggest a Listing
LFM About Us Our Mission Giving Back Contact Us
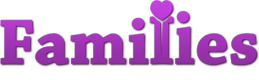
TERMS & CONDITIONS Privacy | Terms
ISSN (ONLINE) 2291-1677
ISSN (PRINT) 2291-1677
Website by ZENxDESIGN